LASER CUTTING
DESCRIPTION
is a technology that uses a laser to vaporize materials, resulting in a cut edge. While typically used for industrial manufacturing applications, it is now used by schools, small businesses, architecture, and hobbyists. Laser cutting works by directing the output of a high-power laser most commonly through optics. The laser optics and CNC (computer numerical control) are used to direct the material or the laser beam generated. A commercial laser for cutting materials uses a motion control system to follow a CNC or G-code of the pattern to be cut onto the material. The focused laser beam is directed at the material, which then either melts, burns, vaporizes away, or is blown away by a jet of gas,[1] leaving an edge with a high-quality surface finish.

YEAR
2021
MONTH
December
PLATFORM
CNC V8
Process
Generation of the laser beam involves stimulating a lasing material by electrical discharges or lamps within a closed container. As the lasing material is stimulated, the beam is reflected internally by means of a partial mirror, until it achieves sufficient energy to escape as a stream of monochromatic coherent light. Mirrors or fiber optics are typically used to direct the coherent light to a lens, which focuses the light at the work zone. The narrowest part of the focused beam is generally less than 0.0125 inches (0.32 mm) in diameter. Depending upon material thickness, kerf widths as small as 0.004 inches (0.10 mm) are possible.[6] In order to be able to start cutting from somewhere other than the edge, a pierce is done before every cut. Piercing usually involves a high-power pulsed laser beam which slowly makes a hole in the material, taking around 5–15 seconds for 0.5-inch-thick (13 mm) stainless steel, for example.
The parallel rays of coherent light from the laser source often fall in the range between 0.06–0.08 inches (1.5–2.0 mm) in diameter. This beam is normally focused and intensified by a lens or a mirror to a very small spot of about 0.001 inches (0.025 mm) to create a very intense laser beam. In order to achieve the smoothest possible finish during contour cutting, the direction of beam polarization must be rotated as it goes around the periphery of a contoured workpiece. For sheet metal cutting, the focal length is usually 1.5–3 inches (38–76 mm).
Advantages of laser cutting over mechanical cutting include easier workholding and reduced contamination of workpiece (since there is no cutting edge which can become contaminated by the material or contaminate the material). Precision may be better, since the laser beam does not wear during the process. There is also a reduced chance of warping the material that is being cut, as laser systems have a small heat-affected zone.[8] Some materials are also very difficult or impossible to cut by more traditional means.
Laser cutting for metals has the advantages over plasma cutting of being more precise[9] and using less energy when cutting sheet metal; however, most industrial lasers cannot cut through the greater metal thickness that plasma can. Newer laser machines operating at higher power (6000 watts, as contrasted with early laser cutting machines' 1500 watt ratings) are approaching plasma machines in their ability to cut through thick materials, but the capital cost of such machines is much higher than that of plasma cutting machines capable of cutting thick materials like steel plate.[10]
HOW TO START LASER CUTTING
Drag the desired print into the selection box
-
1. Layering of drawing typing types according to requirements.
-
2. Cutter power setting for each layer of the drawing, generally 80%-90% power for complete cutting.
-
3. Correcting the position of the cut material.
-
4. Start cutting,run the machine.
01 Setting parameters


02 Cutting
-
First you need to calibrate the engraving position to ensure that the laser cutter engraves within the material range
-
After calibration, the software sends a start engraving command to the machine, followed by laser engraving.

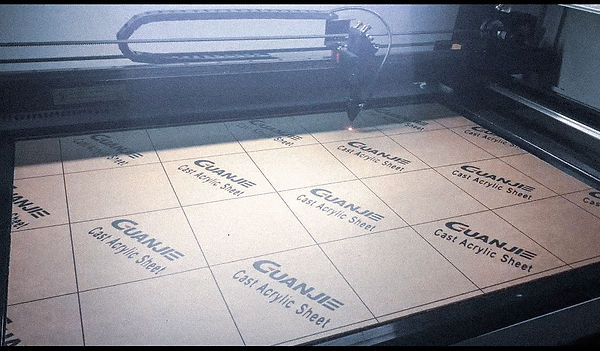
03 Finished
-
After engraving, take out the corresponding parts and assemble them.



04 Assembly
-
Assembly of the printed parts according to the plan

